An investigation on skeleton-based top-down modelling approaches of complex industrial product
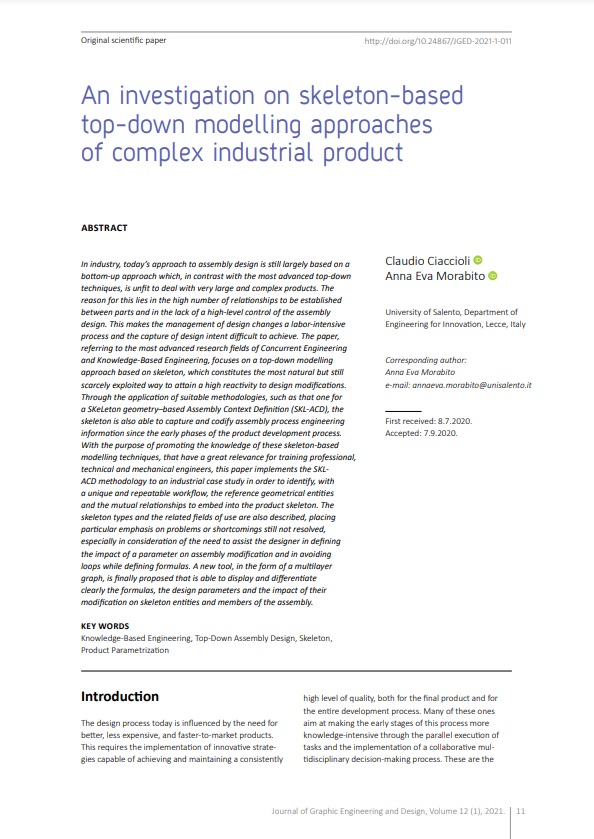
Published 2021-03-01
abstract views: 49 // Full text article (PDF): 45
Keywords
- Knowledge-Based Engineering,
- , Top-Down Assembly Design,
- Skeleton,
- Product Parametrization
How to Cite
Copyright (c) 2021 © 2021 Authors. Published by the University of Novi Sad, Faculty of Technical Sciences, Department of Graphic Engineering and Design. This article is an open access article distributed under the terms and conditions of the Creative Commons Attribution license 3.0 Serbia.

This work is licensed under a Creative Commons Attribution 3.0 Unported License.
Abstract
In industry, today’s approach to assembly design is still largely based on a bottom-up approach which, in contrast with the most advanced top-down techniques, is unfit to deal with very large and complex products. The reason for this lies in the high number of relationships to be established between parts and in the lack of a high-level control of the assembly design. This makes the management of design changes a labor-intensive process and the capture of design intent difficult to achieve. The paper, referring to the most advanced research fields of Concurrent Engineering and Knowledge-Based Engineering, focuses on a top-down modelling approach based on skeleton, which constitutes the most natural but still scarcely exploited way to attain a high reactivity to design modifications. Through the application of suitable methodologies, such as that one for a SKeLeton geometry–based Assembly Context Definition (SKL-ACD), the skeleton is also able to capture and codify assembly process engineering information since the early phases of the product development process. With the purpose of promoting the knowledge of these skeleton-based modelling techniques, that have a great relevance for training professional, technical and mechanical engineers, this paper implements the SKLACD methodology to an industrial case study in order to identify, with a unique and repeatable workflow, the reference geometrical entities and the mutual relationships to embed into the product skeleton. The skeleton types and the related fields of use are also described, placing particular emphasis on problems or shortcomings still not resolved, especially in consideration of the need to assist the designer in defining the impact of a parameter on assembly modification and in avoiding loops while defining formulas. A new tool, in the form of a multilayer graph, is finally proposed that is able to display and differentiate clearly the formulas, the design parameters and the impact of their modification on skeleton entities and members of the assembly.
Article history: Received (July 8, 2020); Revised (August 27, 2020); Accepted (September 7, 2020); Published online (March 1, 2021)